plastic filament extruding machine melt pump
The plastic filament extruder melt pump is one of the crucial equipment in the plastic processing industry. Its main function is to provide stable conveying pressure in the molten plastic state, ensuring that the plastic melt flows uniformly and continuously into the mold during the extrusion process, thereby producing high-quality plastic filaments. The design and performance of the melt pump are directly related to the production efficiency, product quality, and cost control of the extruder.
In the plastic filament extrusion production line, the melt pump is a crucial equipment. Its main function is to provide stable and continuous melt pressure in the molten state of plastic, thereby ensuring the uniform extrusion of plastic filaments. Therefore, selecting a suitable melt pump has a decisive impact on the stability of the production line and product quality.
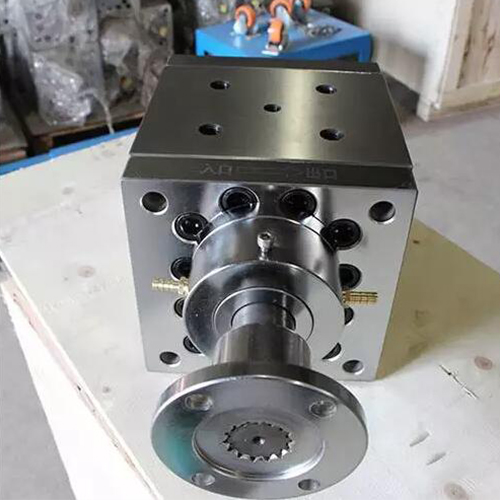
Firstly, we need to understand the basic principles and types of melt pumps. Melt pumps typically consist of an electric motor, a reducer, and a pump body. Among them, the pump body is the key part, which pushes the melt to the outlet through rotating screws or blades. According to the structure and working principle of the pump body, melt pumps can be divided into several types, including screw pumps, gear pumps, and vane pumps. Different types of melt pumps have different characteristics and applicable ranges, so when selecting, it is necessary to consider the specific needs of the production line.
Secondly, key parameters to consider when selecting a melt pump include flow rate, pressure, temperature, viscosity, etc. Flow rate refers to the volume of molten material that a melt pump can transport per unit time, which directly determines the production capacity of the production line. Pressure refers to the outlet pressure that the melt pump can provide, which determines the extrusion speed and product quality of plastic filaments. Temperature and viscosity are related to the type and melting state of plastics, and different types of plastics have different requirements for melt pumps. Therefore, when selecting a melt pump, it is necessary to comprehensively consider these parameters to ensure that the selected pump type can meet the needs of the production line.
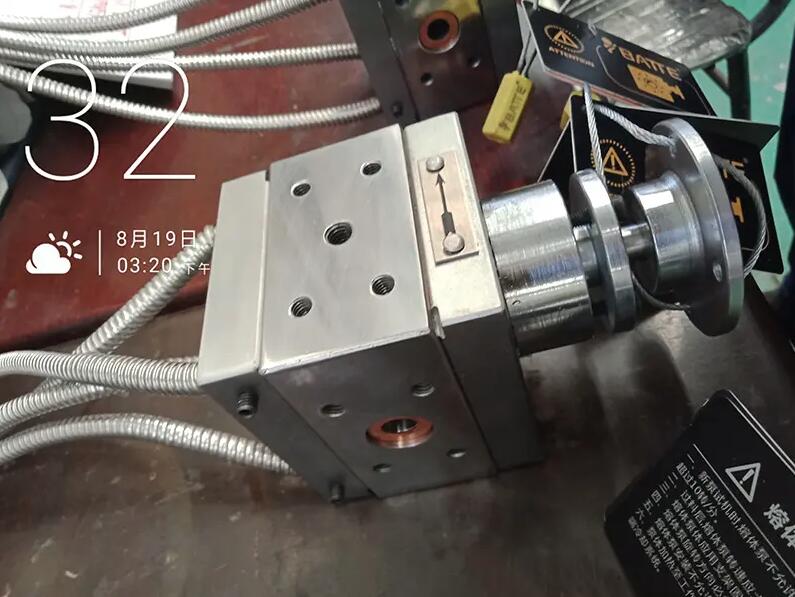
In addition, the quality and performance of the melt pump are also important factors to consider when selecting. A high-quality melt pump should have stable operating performance, good sealing performance, and wear resistance. At the same time, it should also have the characteristics of easy maintenance and upkeep to reduce downtime and repair costs of the production line. Therefore, when choosing a melt pump, it is necessary to choose a brand and supplier with good reputation and after-sales service guarantee.
Finally, selecting a melt pump also requires consideration of the overall layout and process flow of the production line. For example, the installation position of the melt pump needs to be easy to operate and maintain, while also considering its connection method and sealing performance with upstream and downstream equipment. In addition, the optimization of the process flow also needs to be coordinated with the selection of the melt pump to ensure the stability of the production line and product quality.
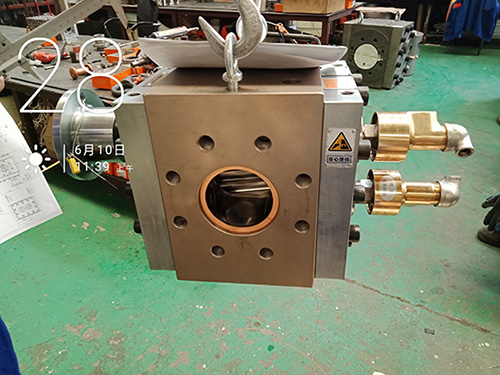
In summary, selecting a suitable melt pump extrusion is crucial for the stability and product quality of plastic filament extrusion production lines. When choosing, it is necessary to comprehensively consider the basic principle and type, key parameters, quality and performance of the melt pump, as well as the overall layout and process flow of the production line. Only in this way can we ensure that the selected melt pump can meet the needs of the production line, improve production efficiency and product quality, and create greater economic value for the enterprise.
Email: info@battemachinery.com
WhatsApp: +86 158 38331071