Working Principle of Polyester Melt Booster Pump
The polyester melt booster pump operates based on the principle of positive displacement, specifically designed for high-temperature, high-viscosity polymer melts. Its core mechanism involves the interaction of meshing gears to alter the working volume, thereby achieving melt transportation and pressurization. Here's a detailed breakdown:
Mechanical Structure:
Rotors: Typically employ helical or spur gears made of nitride steel, tool steel, or stainless steel with coatings. The gears' meshing creates dynamic volume changes.
Housing: Constructed from stainless steel, alloy steel, or corrosion-resistant alloys to withstand high temperatures and pressures.
Sealing: Combines melt dynamic seals with packing or mechanical seals to prevent leakage.
Heating: Utilizes thermal media jackets to maintain melt fluidity, with operating temperatures up to 350°C.
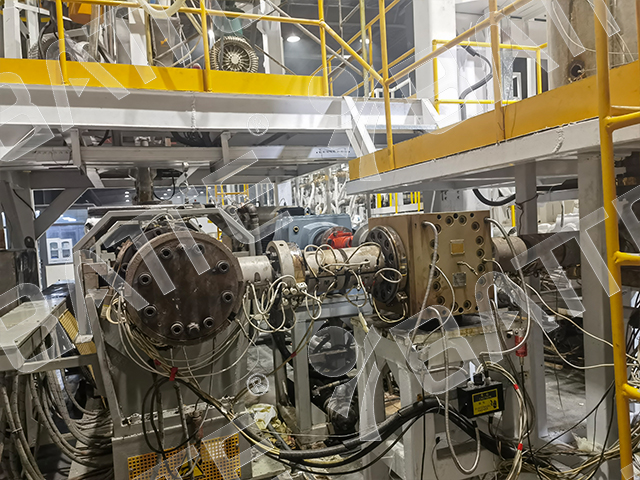
Operational Process:
As the drive gear rotates, melt enters the feed zone between the teeth of the meshing gears.
Continued rotation carries the melt into the discharge zone, where the reducing tooth cavity volume forces the melt out at high pressure.
The pump's outlet pressure can reach 35 MPa, while the inlet pressure requirement is minimal (even vacuum suction is possible).
Control Features:
Flow Regulation: Output flow is directly proportional to pump speed, enabling precise control via variable frequency drives (VFDs).
Pressure Stability: The gear mechanism acts as a rotating barrier, isolating discharge pressure fluctuations from inlet disturbances, ensuring stable melt delivery.
Applications of Polyester Melt Booster Pump
These pumps are critical in industries requiring precise handling of high-temperature polymer melts. Key applications include:
Textile Industry (Fiber Spinning):
Direct Melting Spinning: Pressurizes polyester melts to over 10 MPa before entering the spinneret, ensuring uniform fiber formation.
(Chip Spinning): Metering pumps deliver precise melt volumes for indirect spinning processes.
Process Optimization: Adjusts melt residence time and flow rates during product transitions, enhancing production flexibility.
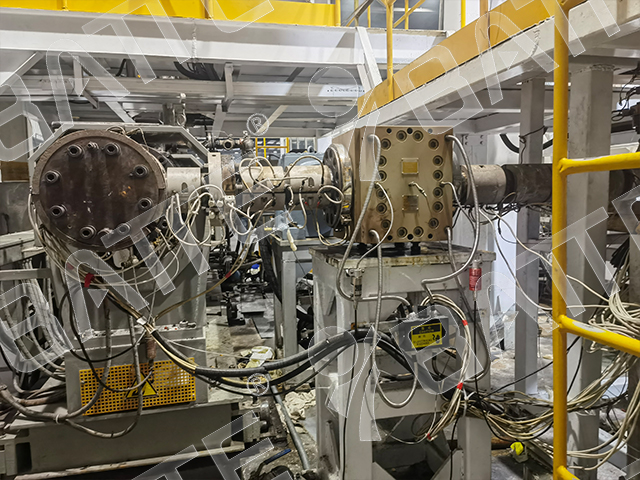
Plastics Manufacturing:
Extrusion Molding: Stabilizes melt pressure in the production of pipes, films, sheets, and profiles. By isolating extruder pressure fluctuations, it improves product dimensional accuracy and surface finish.
Injection Molding: Generates high pressures to fill complex molds efficiently, reducing cycle times and material waste.
Compound Processing: Ensures homogeneous mixing of additives in masterbatch and compound production.
Other Industries:
Resin and Rubber: Handles viscous resins and elastomers in adhesive, coating, and sealant manufacturing.
Medical Devices: Enables precise extrusion of medical-grade plastics for catheters, tubing, and packaging.
Advantages
Efficiency: High-pressure capability reduces energy consumption compared to traditional extrusion methods.
Quality Enhancement: Minimizes melt degradation through controlled shear and residence time.
Versatility: Adaptable to both direct and indirect spinning processes, as well as various extrusion geometries.
Maintenance: Modular design simplifies repairs and reduces downtime.
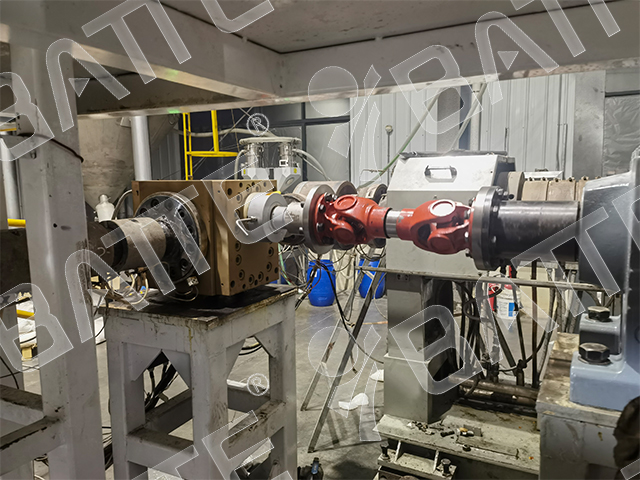
In summary, the polyester melt booster pump's combination of robust construction, precise control, and high-pressure capability makes it indispensable in modern polymer processing, particularly in demanding applications like high-speed spinning and precision extrusion.
Email: sale@meltpump.com
WhatsApp: +86 158 38331071