Double-Ended Sealed Melt Pump
The double-ended sealed melt pump is a specialized type of melt pump characterized by its double-ended mechanical seal design. This unique feature ensures stable melt conveyance and prevents leakage in high-temperature, high-pressure environments. Below is a detailed introduction to the double-ended sealed melt pump:
I. Working Principle
The working principle of the double-ended sealed melt pump is similar to that of ordinary melt pumps. It relies on the change in working volume caused by the meshing of the driving and driven gears to convey the melt. During operation, the melt is drawn into the pump's inlet area, then pushed to the discharge area by the rotation of the gears, and finally ejected through the outlet. The double-ended mechanical seal, located at the pump's shaft end, prevents melt leakage.
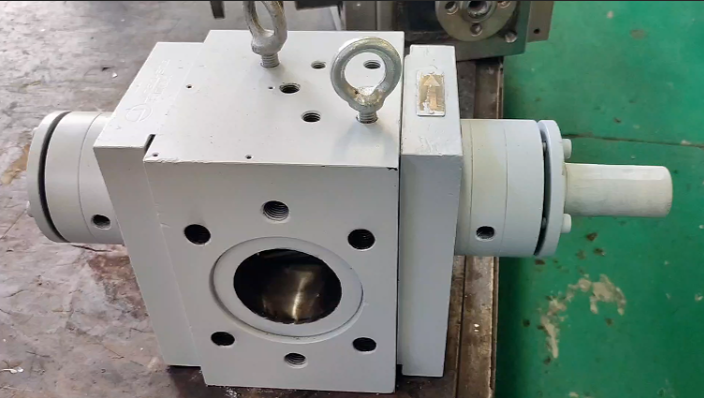
II. Structural Composition
The double-ended sealed melt pump mainly consists of a pump body, driving gear, driven gear, sliding bearings, front and rear end plates, and a double-ended mechanical seal. Among these, the double-ended mechanical seal is the pump's key component, comprising a rotating ring, a stationary ring, elastic devices, auxiliary seals, and a housing. The contact surfaces of the rotating and stationary rings are tightly fitted to form a minute gap. When pressurized media passes through this gap, an extremely thin liquid film forms, preventing media leakage and lubricating the end faces.
III. Sealing Method
The double-ended sealed melt pump employs a double-ended mechanical seal, offering superior sealing performance and longevity. Compared to single-ended mechanical seals, double-ended seals exhibit better adaptability and stability, capable of handling higher working pressures and temperatures. Additionally, they protect the sealing surfaces from damage caused by impurities and particles in the melt, enhancing sealing reliability and durability.
IV. Application Fields
Double-ended sealed melt pumps are widely used in plastic processing, chemicals, pharmaceuticals, and food industries. In plastic processing, they improve extruder productivity and product quality, reducing deformation and defects. In the chemical industry, they convey high-temperature, high-pressure polymer melts like polyethylene and polypropylene. In pharmaceuticals and food processing, they transport high-temperature, high-pressure drugs and food raw materials.
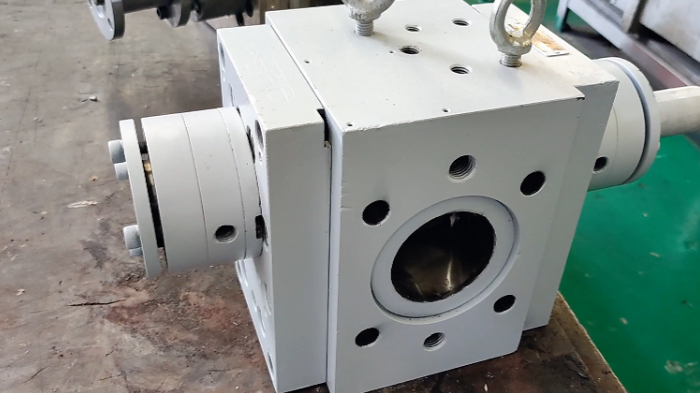
V. Usage Precautions
When installing the double-ended sealed melt pump, ensure concentricity between the pump base and motor drive shaft, and securely fix the pump base. Check the integrity of sealing components and replace worn or aged parts promptly.
Before loading the melt, ensure the pump has reached operating temperature. Start loading at lower speeds and flows, gradually increasing to the required operating conditions.
Regularly monitor the pump's operating status, including flow rate, pressure, and temperature. Address any abnormalities promptly.
Before shutting down, gradually reduce the melt flow and pressure, then close the inlet and outlet valves and motor. Avoid sudden shutdowns that may cause melt solidification or blockage in the pipeline.
Regularly maintain and service the double-ended sealed melt pump, including cleaning and lubrication, to ensure long-term stable operation.
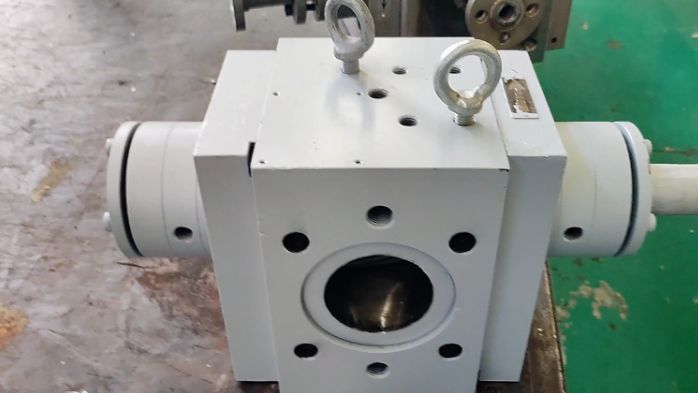
In summary, the double-ended sealed melt pump is a high-performance, high-reliability conveying equipment widely used in various fields. During operation, attention should be paid to installation, loading, monitoring, shutdown, and maintenance to ensure proper function and extend service life.
Email: info@battemachinery.com
WhatsApp: +86 158 38331071