The Application Scope of Melt Pumps for BOPP Film Extruders
The application scope of melt pumps for BOPP film extruders is quite extensive. Below is a detailed introduction to its application scope:
I. Main Application Areas
Plastic Extrusion Industry:
Melt pumps are widely used in the plastic extrusion industry, particularly in the extrusion production of BOPP films. They can pressurize and stabilize the high-temperature plastic melt from the extruder, delivering it steadily to the extruder head, thereby ensuring uniform thickness and stable quality of the film.
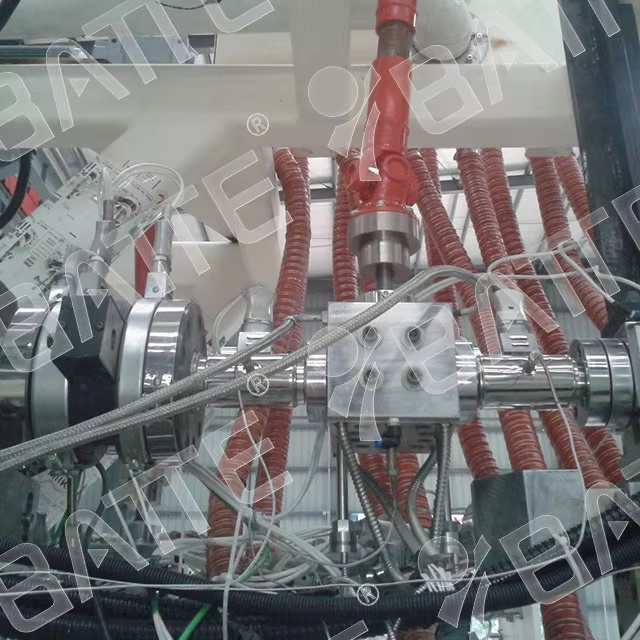
Production of Other Polymer Products:
Apart from BOPP films, melt pumps can also be used to produce other polymer products such as pipes, plates, sheets, artificial fibers, and optical fibers. In these fields, melt pumps similarly stabilize the pressure and flow of the molten material, enhancing the quality and output of the products.
II. Specific Application Scenarios
Improving Product Quality:
In situations where strict dimensional tolerances are required for products or where raw material costs are relatively high, the use of melt pumps can significantly reduce waste rates and improve product acceptability.
Compounding Extrusion Granulation Lines:
Combining a co-rotating twin-screw extruder with a melt pump to form a compounding extrusion granulation line can significantly improve mixing quality and output. Additionally, due to the stabilizing effect of the melt pump, energy consumption can be reduced.
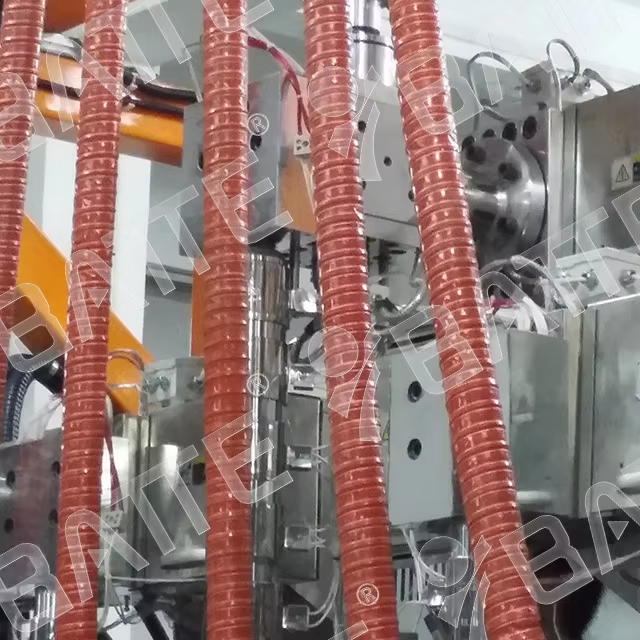
Simplifying Production Processes:
Installing melt pumps and extruder heads for pipes, plates, films, etc., on single-screw or co-rotating twin-screw granulating extruders can eliminate the granulating process and directly extrude products. This system is particularly suitable for materials that require blending and modification during extrusion.
Production of Large-scale Products:
Multiple small-to-medium-sized extruders can simultaneously feed into a single melt pump. The molten material is pressurized and metered by the melt pump before being supplied to the extruder head for the extrusion of large-scale products (such as large-diameter pipes, wide plates, and films). This configuration results in a compact production line with a small footprint, and the cross-sectional dimensions of the extruded products are more precise and easier to control.
III. Technical Features and Advantages
Stable Pressure and Flow:
Melt pumps possess the ability to stabilize the pressure and flow of molten material, superior to various types of extruders. They can eliminate feeding errors from the feeding system and significantly reduce fluctuations transmitted from upstream processes, making the extrusion process more stable.
Increasing Output and Reducing Energy Consumption:
Since melt pumps can transfer the pressure-reducing function of the extruder to the gear pump, the extruder can operate under low pressure and temperature conditions. This not only reduces leakage flow, increases output, but also lowers energy consumption and extends the lifespan of the machinery.
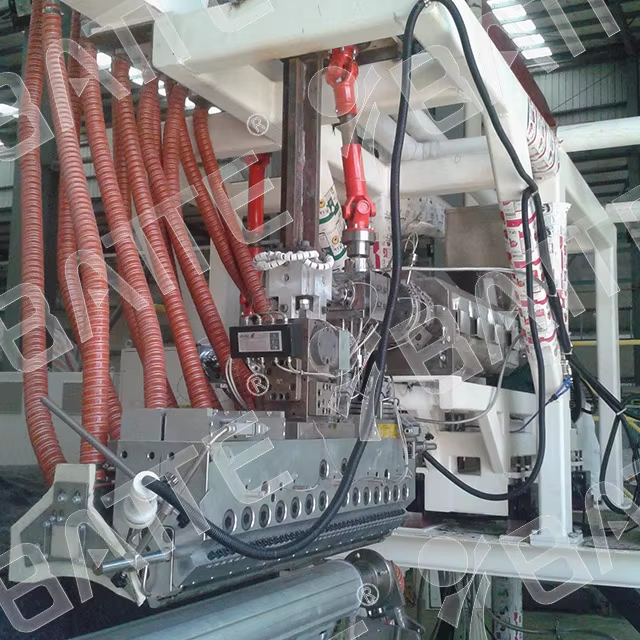
Linear Extrusion Characteristics:
Melt pumps exhibit linear extrusion characteristics, with their conveying capacity being basically linear to their rotational speed. This enables upstream and downstream equipment to coordinate effectively, achieving full-process online monitoring and feedback control throughout the extrusion process.
In summary, melt pumps for BOPP film extruders have a wide range of applications in the plastic extrusion industry and the production of other polymer products. Their advantages of stabilizing pressure and flow, improving product quality and output, and reducing energy consumption make them indispensable equipment in these fields.
Email: info@battemachinery.com
WhatsApp: +86 158 38331071