How to Adjust the Working Pressure of the Melt Pump in a Sheet Extrusion Machine?
Adjusting the working pressure of the melt pump in a sheet extrusion machine primarily relies on a closed-loop control system, precisely tuned in conjunction with material properties and process requirements. Here are some commonly used adjustment methods:
1. Closed-Loop Control Based on Pressure Sensors
Real-time Monitoring:
Pressure sensors are installed at the inlet and outlet of the melt pump to monitor pressure values in real-time.
Variable Frequency Drive Adjustment:
Based on the pressure values monitored by the sensors, the variable frequency drive system adjusts the rotational speed of the melt pump. If the pressure is lower than the set value, the speed is increased to boost pressure; conversely, it is decreased to reduce pressure.
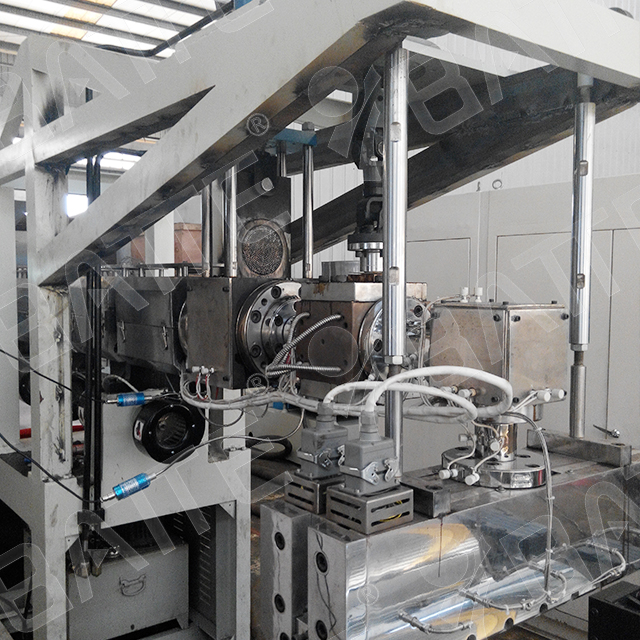
Automatic Adjustment:
If a pressure value is preset, the system will automatically adjust the rotational speed of the melt pump until it reaches and stabilizes at the set value.
2. Inlet Pressure Feedback Control
Pressure Value Feedback:
Based on the pressure value at the inlet of the melt pump, the control system sends feedback information to the extrusion machine.
Material Discharge Control:
According to the feedback information, the control system drives the extrusion machine to adjust the discharge speed and volume, thereby controlling the inlet pressure of the melt pump.
3.Temperature Control
Temperature Monitoring:
The pump body temperature is obtained through sensors on the high-temperature melt pump body.
Heating Equipment Response:
Based on the pump body temperature, the heating equipment responds accordingly to achieve temperature control in response to excessively high or low pressure values.
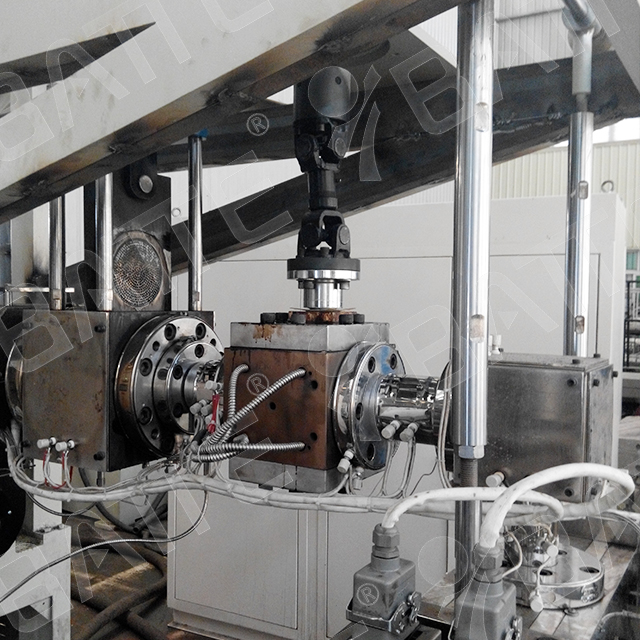
4.Debugging Steps
Preheating:
Begin by preheating the front end, body, and rear section of the melt pump body.
Inspection:
Once the melt pump temperature reaches the set value, remove the motor fan cover and manually rotate the fan blades to drive the melt pump, ensuring there are no jams, abnormal sounds, and smooth rotation.
Manual Adjustment:
Keep the automatic knob in manual mode and set the melt pump frequency to a low level (around 5HZ), with the main machine set to around 3HZ. Gradually increase the main machine frequency while observing changes in inlet pressure.
Automatic Adjustment:
When the pressure reaches the set value, allow it to stabilize for a while before switching to automatic mode.
Fine-tuning of Frequency:
After the main machine switches to automatic, slowly increase the frequency of the melt pump motor in small increments (around 1HZ each time) until the feeding requirements of the die head are met.
Observation and Adjustment:
During the trial run, observe the changes in various parameters of the melt pump. If any abnormalities are detected, turn off the automatic control, investigate the cause, and resolve the issue promptly.
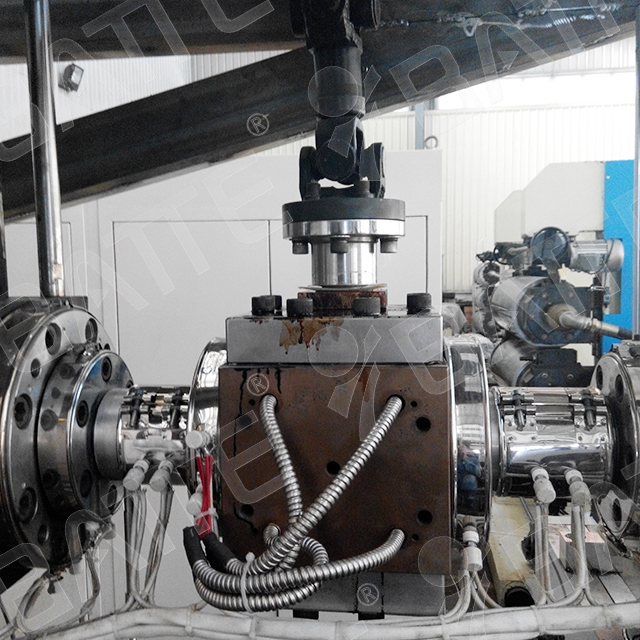
During the adjustment process, closely monitor changes in the melt pump's working pressure, rotational speed, temperature, and other parameters to ensure the equipment operates safely and stably. At the same time, based on production needs and changes in material properties, timely adjust the working pressure, rotational speed, and other parameters of the melt pump to achieve optimal production results.
Email: info@battemachinery.com
WhatsApp: +86 158 38331071