How to Clean and Maintain Plastic Extrusion Melt Pumps for Wire and Cable Production
Cleaning and maintaining plastic extrusion melt pumps for wire and cable production are crucial steps to ensure their stable operation and extend their service life. Below are some detailed guidelines for cleaning and maintenance:
Cleaning Steps
Disassembly of the Pump Body:
Select the appropriate disassembly method based on the actual situation. If there is sufficient operating space and the system can shield the pump section piping, perform disassembly and inspection with the pump still warm to maintain material flow and facilitate the extraction and cleaning of components. If online warm operation is not feasible, disassemble the pump body from the piping and transport it to another location for inspection.
Pay attention to the position and orientation of all components during disassembly to ensure correct reassembly.
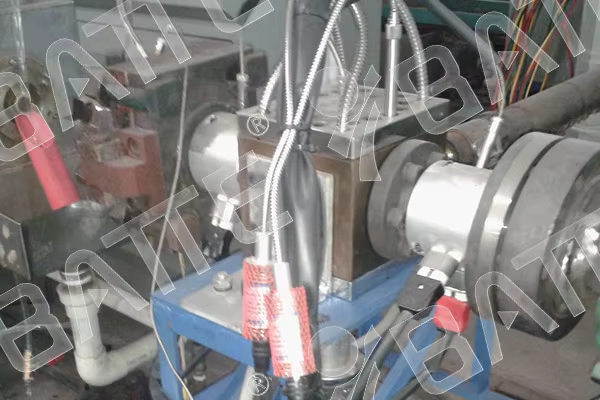
Removal of Residual Material:
If the residual material in the pump has cooled and solidified, use corresponding solvents or presses to remove the solidified material.
Avoid using hard objects to hit or damage the pump body and components during the cleaning process.
Cleaning of Components:
Gently place the removed gears, seals, and other components on a clean surface. Use compressed air or a clean cotton cloth to clean each component.
Carefully inspect each component for wear, cracks, burrs, and scratches. Use 600# sandpaper to gently polish surface attachments, but be particularly careful with key components such as metering gears, middle plates, and D-type bearings, avoiding removing metal or grinding them.
Clean all components with trichloroethane or vinyl chloride solvent and then wipe them clean with a cotton cloth. Avoid using paper towels to prevent paper fibers or impurities from adhering to the components.
Maintenance Steps
Regular Inspection and Lubrication:
Regularly inspect the bearings, seals, and other wearing parts of the melt pump to ensure their wear is within the allowable range.
Lubricate bearings and other components to reduce friction and wear.
Keeping the Pump Body Clean:
Regularly clean the external dust and dirt from the pump body to keep it clean and tidy.
Avoid exposing the pump body to high temperatures or humid environments for extended periods to prevent corrosion and damage.
Inspection and Adjustment of Sealing:
Regularly inspect the sealing of the melt pump to ensure there are no leaks.
For melt pumps with gland packing seals, adjust the position of the sealing gland in a timely manner to ensure optimal sealing.
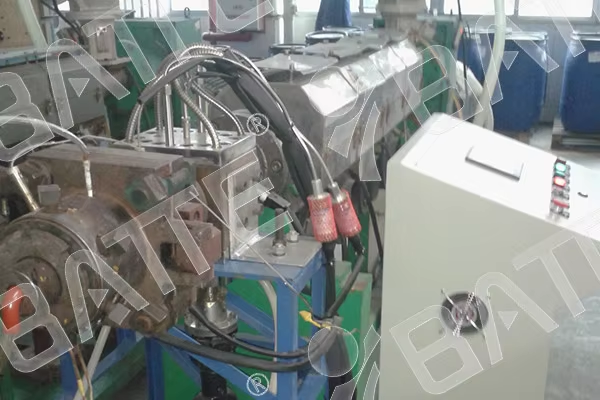
Maintaining the Electrical System:
Regularly inspect the electrical system of the melt pump, including the motor and cables, to ensure they are free from damage and aging.
Maintain good electrical connections to avoid loosening and short circuits.
Regular Calibration and Testing:
Regularly calibrate and test the melt pump to ensure its output flow rate, pressure, and other parameters meet requirements.
Investigate and repair any abnormalities promptly.
Safe Operation and Maintenance:
Follow relevant safety operating procedures during cleaning and maintenance.
Avoid cleaning and maintenance work while the pump body is operating to prevent danger.
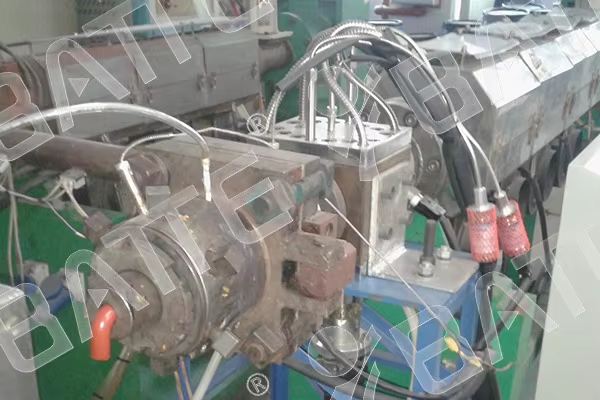
Precautions
Use appropriate tools and materials during cleaning and maintenance to avoid damaging the pump body and components.
Ensure all components are correctly installed and securely fastened after cleaning and maintenance.
Regular maintenance and upkeep of the melt pump can help identify and resolve issues promptly, ensuring stable operation and extending service life.
In summary, cleaning and maintaining plastic extrusion melt pumps for wire and cable production requires following specific steps and precautions. Correct cleaning and maintenance practices contribute to the normal operation and extended service life of the melt pump.
Email: info@battemachinery.com
WhatsApp: +86 158 38331071