Application Scheme of Melt Pumps in Plastic Broom Production Lines
The application scheme of melt pumps in plastic broom production lines aims to enhance production efficiency and ensure product quality by precisely controlling the pressure and flow rate of the melt. Below is a detailed application scheme:
I. Selection of Melt Pump
Flow Rate and Pressure Requirements:
Determine the required melt flow rate and pressure range based on the specific needs of the plastic broom production line.
Select a melt pump with an appropriate flow rate and pressure range to meet the extrusion demands of the production line.

Material Compatibility:
Consider the type and characteristics of the plastic raw materials and choose a melt pump material that is compatible with them.
Ensure that the melt pump does not contaminate or degrade the plastic raw materials during transportation.
Reliability and Durability:
Choose a melt pump with excellent reliability and durability to reduce downtime and maintenance costs.
Consider the material and manufacturing process of critical components such as gears and bearings to ensure they can withstand high-temperature and high-pressure working environments.
II. Installation and Commissioning of Melt Pump
Installation Location:
Install the melt pump downstream of the extruder to ensure that the melt undergoes pressure boosting and stabilization before extrusion.
Ensure that the installation location of the melt pump is convenient for operation and maintenance.
Piping Connection:
Use high-temperature and high-pressure resistant piping to connect the melt pump and extruder.
Ensure that the piping connections are well-sealed to avoid melt leakage.
Commissioning and Testing:
After installation, commission and test the melt pump.
Adjust the melt pump's rotational speed and pressure settings to meet the production line's requirements.
Check the lubrication and cooling systems of the melt pump to ensure they are functioning properly.
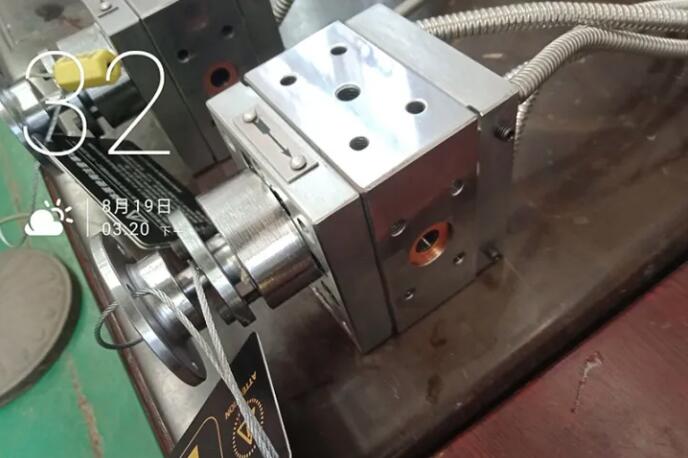
III. Operation and Maintenance of Melt Pump
Operation Monitoring:
Continuously monitor the operating status of the melt pump during production.
Pay attention to parameters such as the melt pump's pressure, flow rate, and temperature to ensure they are within normal ranges.
Regular Maintenance:
Regularly maintain and service the melt pump.
Check the wear of critical components such as gears and bearings, and replace damaged parts promptly.
Clean the pump body and piping of the melt pump to avoid clogging and contamination.
Fault Handling:
Immediately shut down and inspect the melt pump if any faults or abnormalities are detected.
Take appropriate corrective measures based on the fault type, such as replacing damaged parts or adjusting setting parameters.
IV. Application Effect Evaluation
Production Efficiency:
Evaluate the improvement effect on the production line by comparing production efficiency before and after using the melt pump.
Observe the continuity and stability of the production line to ensure that the melt pump can consistently provide stable melt flow rate and pressure. Product Quality:
Inspect the quality of plastic brooms produced after using the melt pump.
Assess the impact of the melt pump on product quality, such as dimensional accuracy and surface quality.
Energy Consumption and Cost:
Monitor energy consumption after using the melt pump.
Evaluate the impact of the melt pump on production costs, including equipment investment and maintenance costs.
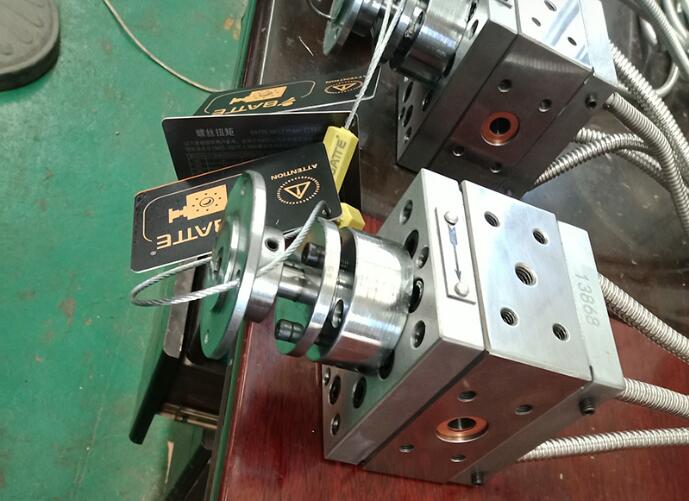
In summary, the application scheme of melt gear pumps in plastic broom production lines requires comprehensive consideration of selection, installation and commissioning, operation and maintenance, as well as application effect evaluation. By reasonably applying melt pumps, production efficiency can be significantly improved, product quality ensured, and production costs reduced.
Email: info@battemachinery.com
WhatsApp: +86 158 38331071