Plastic casting film extrusion melt pump
The Plastic Cast Film Extrusion Melt Pump is a crucial piece of equipment in the process of plastic cast film extrusion. Below is a detailed introduction to this equipment:
I. Definition and Working Principle
The Plastic Cast Film Extrusion Melt Pump, simply known as the melt pump, is a precision pumping device. It utilizes rotating screws or gears to stably and uniformly convey high-viscosity plastic melt to the downstream extruder head. Its working principle mainly relies on the rotation of screws or gears, transporting the melt by changing the working volume. When the screws or gears rotate in the prescribed direction, the melt is drawn in and conveyed to the outlet along with the rotation, achieving stable flow rate and pressure control.
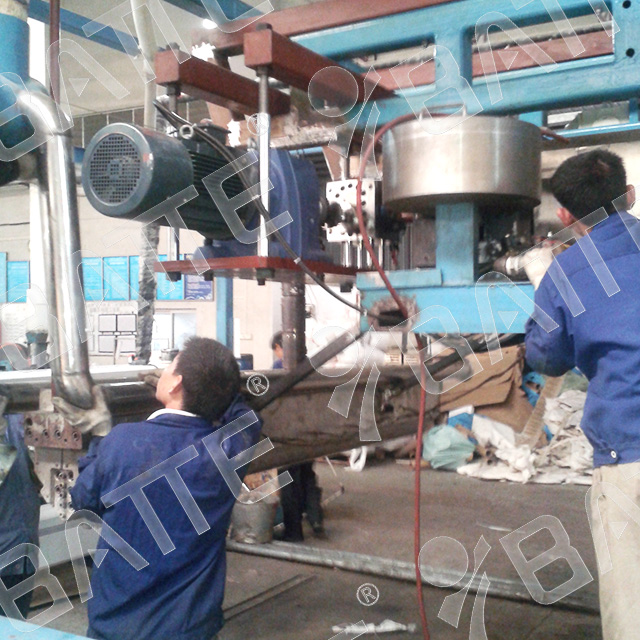
II. Application Scenarios
The melt pump has a wide range of applications in the plastic cast film extrusion process. It is primarily used to pressurize and stabilize the high-temperature plastic melt from the extruder before sending it to the extruder head, ensuring the stability and consistency of the film. In the production of high-performance films, high-precision transparent films, and films requiring controlled parameters such as color, thickness, and density, the melt pump plays an irreplaceable role.
III. Main Advantages
High Precision: The melt pump can precisely adjust the flow rate and temperature of the melt, meeting the high-precision requirements of plastic cast film manufacturing.
Stable Transportation: Through stable and balanced conveyance and pressurization, the melt pump ensures stable melt transportation, avoiding fluctuations and instability during the extrusion process.
Energy Saving and Consumption Reduction: The melt pump does not require additional energy consumption and can directly convey the melt to downstream equipment, thereby saving energy resources.
Increased Production Efficiency: The melt pump can accurately adjust the flow rate and temperature of the melt, avoiding issues such as low production efficiency and unstable output caused by traditional production methods.
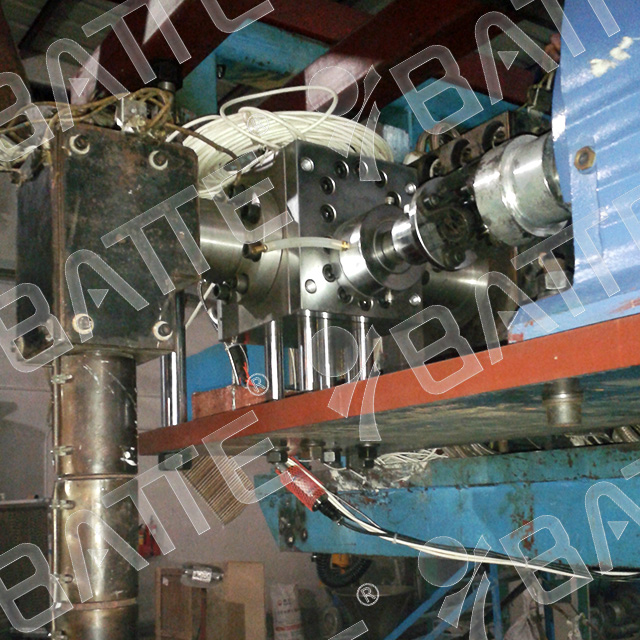
IV. Technical Parameters and Selection
The technical parameters of the melt pump include melt viscosity, melt temperature, outlet pressure, and flow range. When selecting a melt pump, it is necessary to determine the appropriate model and specification based on specific production requirements, the type of extruder, and the characteristics of the melt.
V. Maintenance and Servicing
To ensure the long-term stable operation of the melt pump, regular maintenance and servicing are required. This includes cleaning the pump body, checking the wear of screws or gears, replacing worn parts, and lubrication. Additionally, attention should be paid to the temperature and pressure control of the melt to avoid damage to the melt pump from excessively high or low temperatures and pressures.
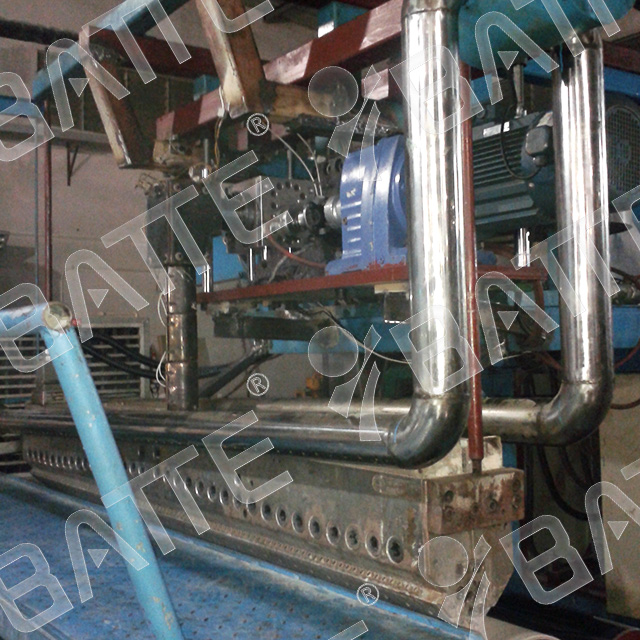
In summary, the Plastic Cast Film Extrusion Polymer Melt Pump is one of the important equipment in the field of plastic film manufacturing. By precisely controlling the flow rate and temperature of the melt, it ensures the stability and consistency of the film, improves production efficiency, and reduces energy consumption. With technological advancements and development, the application prospects of melt pumps in the field of plastic film manufacturing will become even broader.
Email: info@battemachinery.com
WhatsApp: +86 158 38331071