Disadvantages and application scope of HDPE blown film melt pump
The HDPE blown film melt pump is a dedicated melt pump for conveying and processing polymers such as HDPE (High-Density Polyethylene) and other high-molecular-weight materials. Below is a detailed introduction to the disadvantages and application scope of the HDPE blown film melt pump:
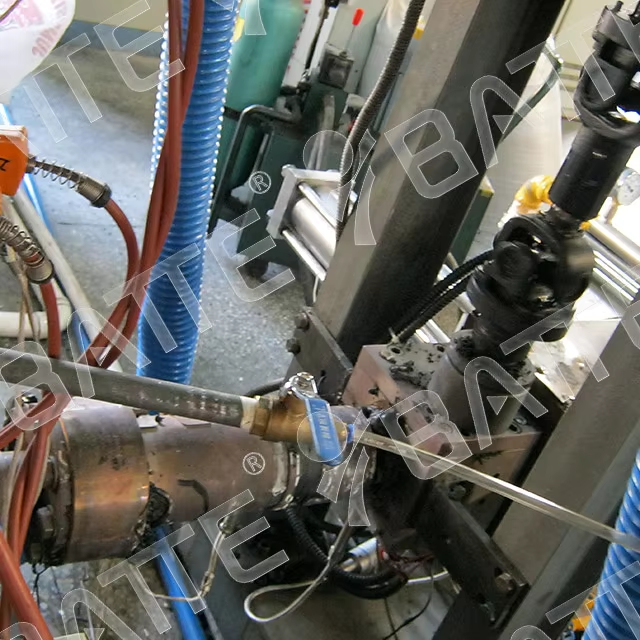
I. Disadvantages
High Maintenance Costs: The melt pump requires regular maintenance and repairs to ensure its normal operation. Due to its relatively complex structure, it may require a higher level of technical expertise and more time and effort for maintenance and repairs.
Relatively High Manufacturing Cost: The manufacturing cost of the melt pump is relatively high, resulting in a larger initial investment. Enterprises need to select and configure the pump based on production demands to fully utilize its performance and reduce costs.
Specific Material Requirements:
The application of the melt pump is limited when processing plastics containing fillers or special modifiers. It has strict requirements on the dispersion of components, compatibility with plastics, and abrasiveness.
Materials containing large particles, abrasive fillers, or reinforcing agents cannot be processed using extruders equipped with melt pumps. This is because the included filler particles can easily form plugs that cannot pass through the gear tooth clearance of the melt pump's meshing gears, and plug blockages and abrasive wear on the teeth can quickly damage the melt pump.
Finely dispersed mineral fillers may also gradually form plugs that can damage the melt pump when they are not well compatible with plastics in high-speed shear zones.
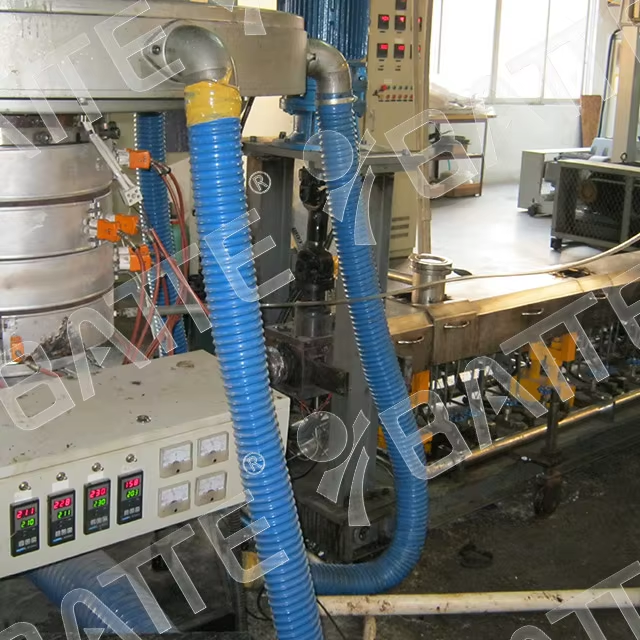
II. Application Scope
Engineering Plastics and Blown Film Processes: The HDPE blown film melt pump is particularly suitable for the blown film process of engineering plastics, such as HDPE (High-Density Polyethylene) and other high-pressure conditions.
High-Pressure Conditions: This pump can withstand high pressures, with a maximum inlet pressure of 20 MPa, a maximum outlet pressure of 70 MPa, and a maximum pressure difference of 50 MPa. It is suitable for high-pressure extrusion conditions.
Production of High-Quality Products: Due to the melt pump's ability to stabilize melt pressure and flow rate, reducing fluctuations, it is suitable for producing high-quality products, especially those with uniform thickness. When extruding thin films and thin-walled profiles, the use of a melt pump yields better results.
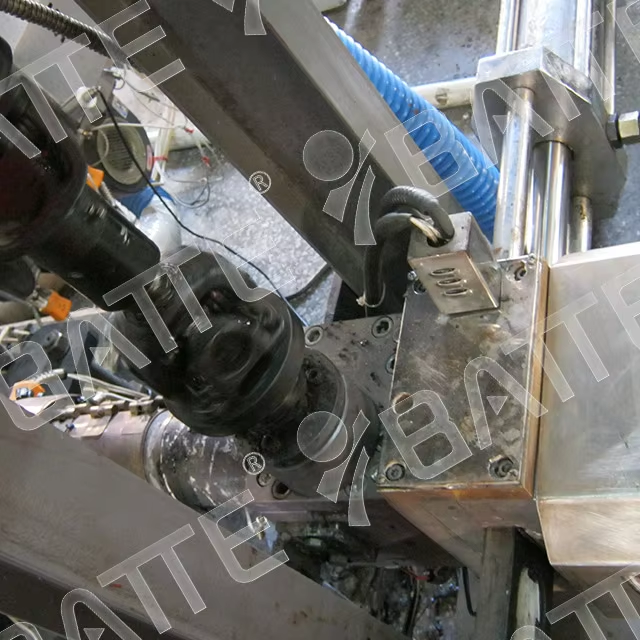
In summary, despite its disadvantages, the HDPE blown film melt pump's efficiency and stability make it an important equipment in the blown film process of engineering plastics. When selecting and using it, enterprises should fully consider factors such as production demands, material characteristics, pump maintenance, and costs.
Email: info@battemachinery.com
WhatsApp: +86 158 38331071