What is the maintenance cost of the melt pump?
The maintenance cost of melt pumps varies due to multiple factors, including pump type, specifications, operating environment, maintenance intervals, material selection, and operational methods. Therefore, it is not feasible to provide a specific numerical figure for maintenance costs. However, we can explore the influencing factors of melt pump maintenance costs from the following aspects:
I. Equipment Selection and Specifications
Pump Type and Specifications: Different types of melt pumps (such as gear pumps, screw pumps, etc.) differ in their structures and maintenance requirements. Generally, larger pumps tend to have higher maintenance costs.
Material Selection: The materials used for critical components like the pump body, pump shaft, bearings, and seals directly impact the pump's lifespan and maintenance costs. Adopting materials that are resistant to high temperatures and wear can extend the pump's lifespan and reduce maintenance frequency.
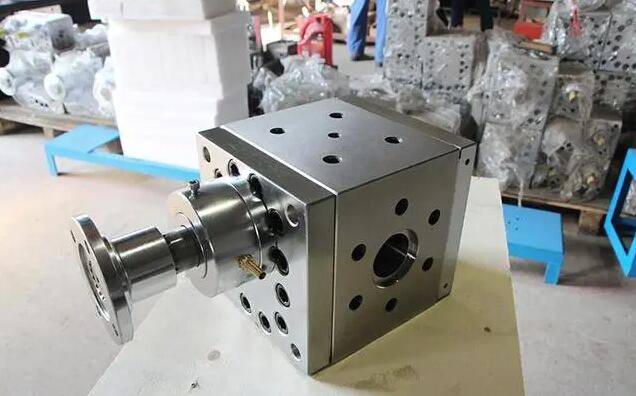
II. Operating Environment
Operating Temperature and Pressure: Melt pumps operate under high temperatures and pressures, demanding high temperature and pressure resistance from their components. Harsh operating environments can accelerate component wear and increase maintenance costs.
Media Characteristics: The viscosity, corrosivity, and solid content of the melt also affect pump maintenance costs. High viscosity, corrosive, or high solid content media can exacerbate pump wear and cause clogging.
III. Maintenance Intervals and Methods
Regular Maintenance: Regularly conducting inspections, cleaning, lubrication, and replacing wear parts for melt pumps can effectively reduce failure rates and extend pump lifespans. The setting of maintenance intervals should be based on equipment usage and manufacturer recommendations.
Preventive Maintenance: Utilizing online monitoring and fault diagnosis systems to identify potential issues in advance and implement preventive measures can reduce downtime and maintenance costs caused by sudden failures.
IV. Components of Maintenance Costs
Labor Costs: Including wages, benefits, and training expenses for maintenance personnel.
Material Costs: Expenses for replacing wear parts (such as bearings, seals, gears, etc.) and consumables (like lubricants, cleaning agents, etc.).
Other Costs: Including transportation fees, taxes, and insurance premiums.
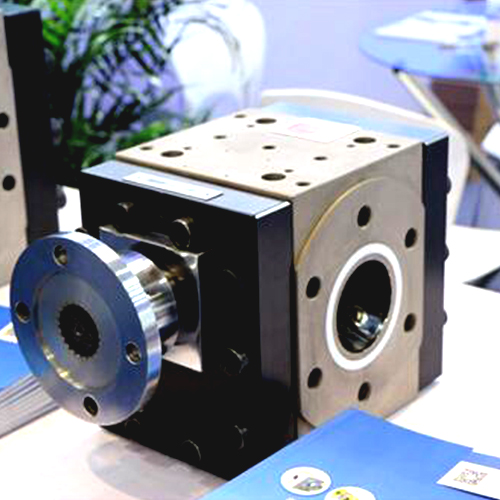
V. Strategies to Reduce Maintenance Costs
Optimize Selection: Choose the appropriate melt pump type and specifications based on actual needs to avoid over-investment.
Improve Operational Skills: Strengthen training and management of operators to enhance equipment efficiency and stability.
Strengthen Maintenance and Servicing: Develop and strictly implement scientifically reasonable maintenance and servicing plans.
Introduce Advanced Technology: Employ advanced online monitoring and fault diagnosis systems to achieve intelligent equipment management.
In conclusion, the maintenance cost of melt pumps is a complex issue requiring comprehensive consideration from multiple angles. To reduce maintenance costs, enterprises should formulate reasonable maintenance strategies and management systems based on their own circumstances.
Email: info@battemachinery.com
WhatsApp: +86 158 38331071