Meltblown fabric extrusion melt pump
When selecting a melt-blown extrusion melt pump, several factors need to be considered to ensure that the pump's performance meets production needs and to ensure the stable operation of the equipment. Here are some key selection factors and considerations:
I. Understand the basic types and characteristics of melt pumps
The melt pump, also known as a high-temperature melt pump or melt-blown fabric metering pump, is a positive displacement pump used to transport high-viscosity, high-temperature melts. It relies on the mutual engagement of the driving and driven gears to create changes in the working volume, thereby transporting the melt. The melt pump has the characteristics of high output pressure, high viscosity of the conveying medium, high operating temperature, and convenient speed adjustment.
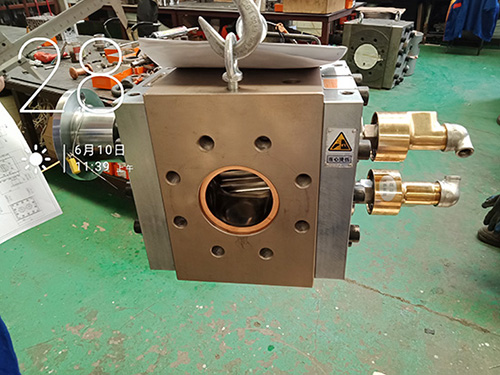
II. Clarify production requirements and working conditions
Production demand: Select the appropriate melt pump specifications based on the production demand of the melt blown fabric production line. The production demand determines the flow requirement of the pump.
Material characteristics: understand the viscosity, temperature, corrosivity, and other characteristics of melt-blown fabric raw materials. These characteristics will directly affect the material selection, sealing method, and operational stability of the pump.
Operating temperature: The range of operating temperatures during the production process of meltblown fabric to ensure that the pump can operate stably within this temperature range.
Import and export pressure: Define the pressure requirements for the inlet and outlet of the melt pump, so as to select a pump type that can withstand the pressure.
III. Selecting the appropriate pump type and specifications
Pump type selection: Select the appropriate melt pump type based on production requirements. Common types of melt pumps include spur gear pumps, helical gear pumps, and herringbone gear pumps. Different pump types vary in terms of delivery efficiency, pressure stability, noise control, and other aspects.
Specification determination: Determine the specific specifications of the melt pump based on production volume, material characteristics, and working pressure requirements. including parameters such as pump flow, pressure, speed, and motor power.
Fourth, consider the material and sealing method of the pump
Pump body material: Select high temperature, wear-resistant, and corrosion-resistant materials as the pump body material to ensure stable operation of the pump under harsh conditions. Common materials include alloy steel, stainless steel, etc.
Sealing method: Select the appropriate sealing method based on the material properties and working conditions. Common sealing methods include packing seal, mechanical seal, etc. For high viscosity and high temperature melts, melt self-lubrication is usually used to avoid contaminating the melt.
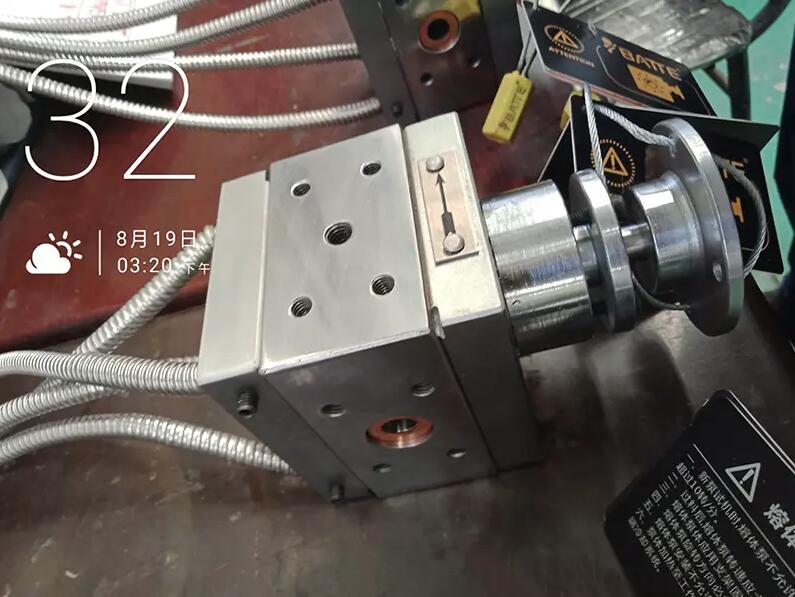
V. Pay attention to the drive and control mode of the pump
Driving mode: Melt pumps are usually driven by motors, which are connected to the pump body through reducers and couplings. It is recommended to use a universal coupling to connect the reducer and the melt pump to eliminate the impact of thermal deformation.
Control method: The melt pump can adjust the output flow by adjusting the speed. It is recommended to adopt frequency control to achieve a nearly linear flow output of the melt pump. This method can more accurately control the flow and pressure, improve production efficiency and product quality.
VI. Other precautions
Brand and manufacturer selection: choose a well-known brand and a reputable manufacturer to produce melt pumps to ensure product quality and after-sales service.
Installation and commissioning: During installation and commissioning, the equipment manufacturer's operation manual and maintenance guide should be followed. Ensure that the pump body is installed horizontally, the inlet and outlet pipelines are connected tightly, and the sealing is good.
Maintenance and upkeep: Regularly maintain and upkeep the melt pump, including checking the wear of seals and bearings, cleaning the pump chamber and inlet and outlet pipes, etc. This helps to extend the service life of the pump and maintain its stable operation.
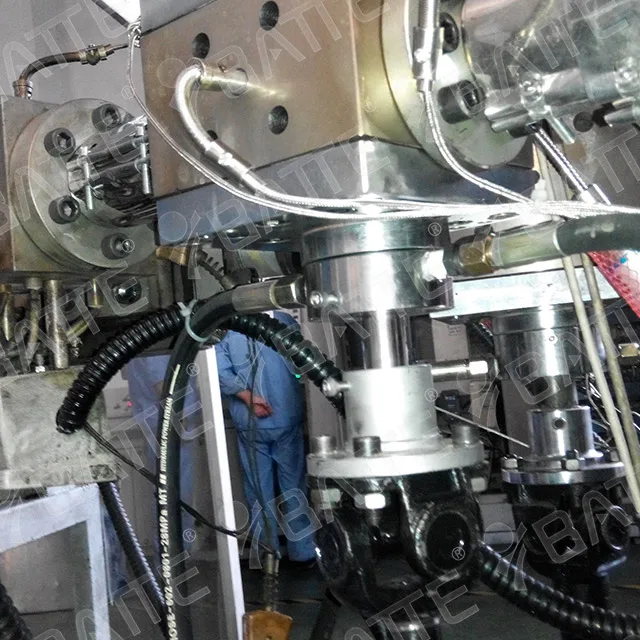
In summary, when selecting a melt-blown extrusion melt pump, several factors need to be considered, including production requirements, operating conditions, pump specifications, material sealing methods, and drive control methods. By comprehensively considering these factors and selecting the appropriate pump type and specifications, it is possible to ensure stable operation and efficient production of melt pumps in the production process of melt-blown fabrics.
Email: info@battemachinery.com
WhatsApp: +86 158 38331071