How do the gears of the melt pump mesh
The gear meshing method of the melt pump is the core part of its working principle, mainly relying on the mutual meshing of two or more gears to achieve the transportation and pressurization of the melt. The following is a detailed explanation of the gear meshing method of the melt pump:
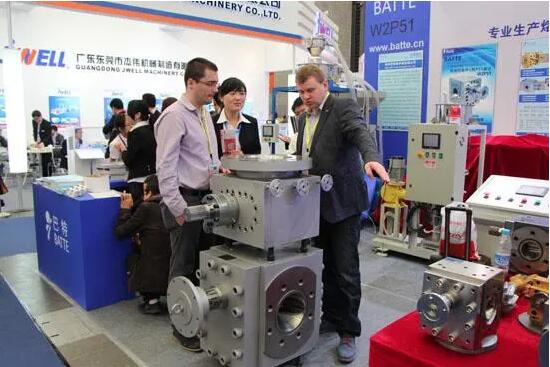
1、 Basic structure
The basic structure of a melt pump is usually an external meshing gear pump, which consists of two meshing gears with the same module, number of teeth, and tooth width, rotating in a pump body that precisely matches their outer diameter and end face. This structure ensures that the gears can stably mesh and effectively transport the melt during rotation.
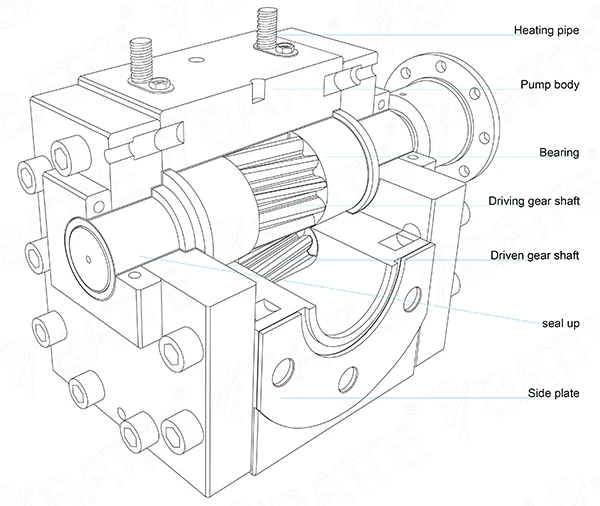
2、 Meshing method
External meshing: The most common meshing method in melt pumps is external meshing. In this way, the teeth of the two gears interlock with each other, forming a series of sealed chambers. As the gears rotate, these chambers gradually move from the inlet side to the outlet side of the pump, thereby achieving continuous transport of the melt.
Internal meshing: Although internal meshing is not as common as external meshing in melt pumps, it is still an effective meshing method. Internal gear pumps typically consist of an internal gear and an external gear, which mesh with each other inside the pump body. However, due to the relatively complex structure and high manufacturing cost of internal gear pumps, their application in the field of melt conveying is relatively limited.
3、 Tooth profile curve and tooth orientation
The gears of the melt pump can also be classified according to the tooth profile curve and tooth direction. Common tooth profile curves include involute gears, circular arc gears, and cycloidal gears; And the tooth direction can be divided into spur gears, helical gears, and herringbone gears. The commonly used external gear pump for conveying plastic melt is the involute spur or helical gear pump.
4、 Meshing process
When the melt pump starts working, two meshing gears rotate inside the pump body. As the gear rotates, the teeth on the left side of the meshing point gradually disengage, increasing the space and forming a local vacuum, continuously sucking the melt into the suction chamber. At the same time, the teeth on the right side of the meshing point gradually enter into meshing, squeezing out the molten material between the teeth. This process is continuously repeated to achieve continuous transportation and pressurization of the melt.
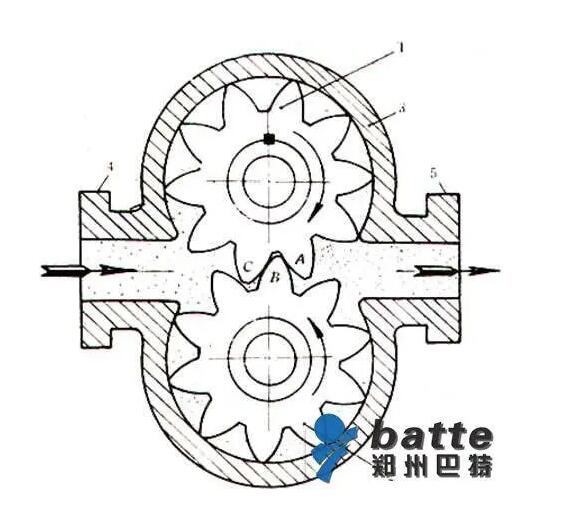
5、 Characteristics and advantages
High stability: The gear meshing method of the melt pump ensures the stability and consistency of melt transportation.
High efficiency: By optimizing gear design and increasing speed, the melt pump can achieve efficient melt transportation and pressurization.
Good temperature resistance: Melt pumps are usually made of high-temperature resistant materials, which can adapt to the transportation needs of high-temperature melts.
Strong sealing: The melt pump uses high-quality sealing materials and sealing structures to ensure that the melt will not leak during transportation.
In summary, the gear meshing method of the melt pump is the key to achieving melt conveying and pressurization. Through external meshing, involute tooth profile curve, and tooth profile design of straight or helical teeth, the melt pump can stably and efficiently transport high-temperature and high viscosity polymer melt.
Email: info@battemachinery.com
WhatsApp: +86 158 38331071