Do PLA PET extrusion production lines need to be equipped with melt pumps and screen changers?
The PLA and PET extrusion production lines do not necessarily require the addition of melt pumps and screen changers, but installing these devices can significantly enhance the performance, product quality, and production efficiency of the lines.
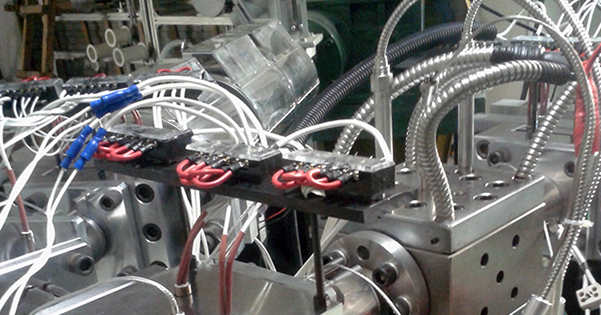
Benefits of Melt Pumps:
Stable Melt Pressure and Flow: Melt pumps can stably increase and maintain the pressure of high-temperature plastic melts and deliver them to the extrusion die at a stable flow rate. This stability helps reduce fluctuations during extrusion, improving product size consistency and quality.
Improved Product Quality: The use of melt pumps can significantly reduce the dimensional tolerances of extruded products, enhancing product precision. They are particularly essential when raw material costs are high or product size requirements are strict.
Increased Production Efficiency: When used in combination with extrusion machines, melt pumps can optimize the extrusion process and improve the overall efficiency of the production line. For example, installing a melt pump on a single-screw or twin-screw extrusion machine allows for direct extrusion of products, eliminating the need for granulation and shortening the production cycle.
Reduced Energy Consumption: The use of melt pumps helps reduce energy consumption during extrusion. By optimizing the extrusion process and minimizing unnecessary energy losses, production costs can be lowered.
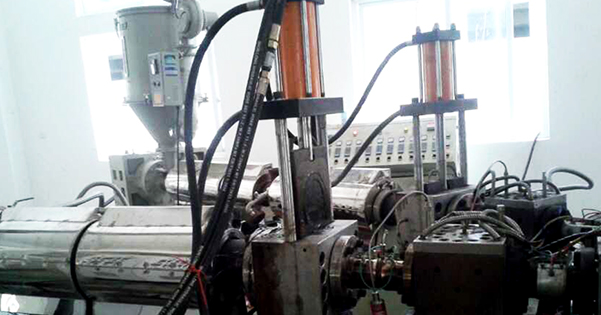
Benefits of Screen Changers:
Impurity Filtration: The primary function of screen changers is to filter impurities and particles from molten materials, ensuring product purity and quality. This is crucial for enhancing the market competitiveness of products.
Enhanced Product Quality: By installing filters of different precision levels, screen changers can accurately remove impurities and particles from the melt, meeting various product process requirements. This helps improve the overall quality and market acceptance of products.
Continuous Production: Modern screen changer designs allow for filter screen replacement without stopping the main extrusion machine, reducing downtime due to screen changes and ensuring continuous production.
Extended Equipment Lifespan: The use of screen changers can reduce wear on internal extrusion machine components caused by impurities, thereby extending equipment lifespan and reducing maintenance costs.
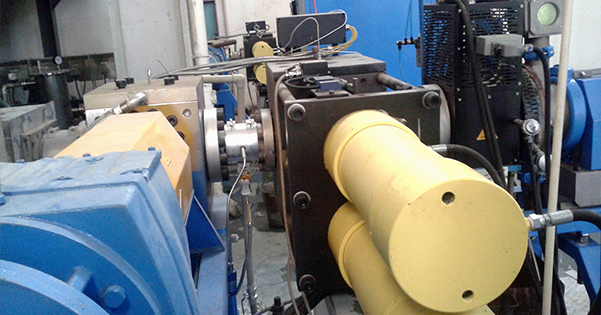
Necessity of Installation:
While melt pumps and screen changers offer numerous benefits to PLA and PET extrusion production lines, whether they are necessary depends on specific production needs and conditions. For instance, in scenarios where raw material purity is high, product size requirements are lenient, or production cost budgets are limited, these devices may not be necessary. However, in pursuit of high quality, efficiency, and market competitiveness, installing melt pumps and screen changers is a wise choice.
In summary, PLA and PET extrusion production lines do not necessarily require the addition of melt pumps and screen changers, but installing these devices can significantly enhance the performance, product quality, and production efficiency of the lines. Enterprises should weigh and choose based on their own needs and conditions.
Email: info@battemachinery.com
WhatsApp: +86 158 38331071