What are the characteristics of the application of melt pumps in the plastic processing industry?
The application of melt pumps in the plastics processing industry is characterized by several notable features, which are primarily embodied in the following aspects:
I. Functional Characteristics
Stable Flow and Pressure:
The melt pump, through its unique gear design, effectively isolates the influence of pressure and flow fluctuations in the feed zone from the discharge zone, achieving stable flow and pressure output. This is crucial for plastic processing processes that require precise control over material flow. The pump's stable output pressure ensures that the plastic melt maintains constant pressure and flow during extrusion, thereby enhancing product dimensional accuracy and surface quality.
High-Pressure Delivery Capability:
The melt pump is capable of generating high pressures to transport high-viscosity melts to desired locations. This is particularly important in processes such as injection molding and extrusion, ensuring smooth extrusion of plastic melts under high pressure to produce high-quality products.
Precise Control:
The melt pump facilitates precise flow control by adjusting its rotational speed. This level of precision is vital for producing high-quality, high-precision plastic products.
High Efficiency:
The melt pump can generate high flow rates at relatively low rotational speeds, thereby improving energy efficiency and production efficiency. This helps to reduce production costs and enhance economic benefits.
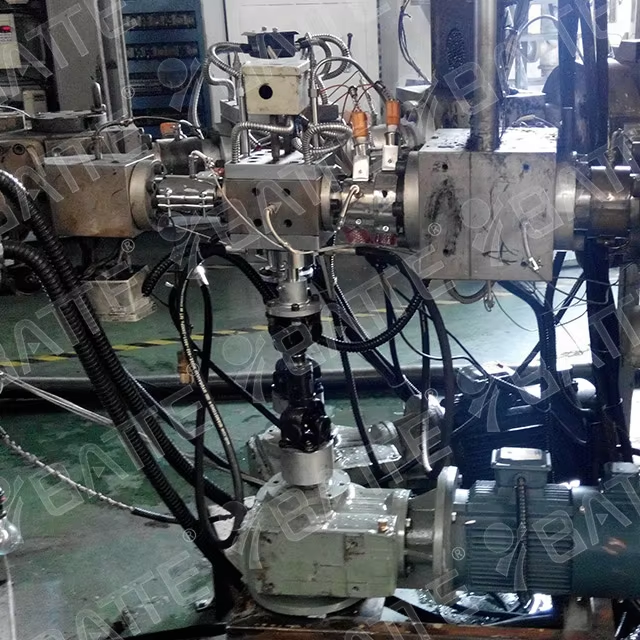
II. Extensive Applicability
Processing of Multiple Plastic Materials:
The melt pump is suitable not only for processing common plastics like PE (polyethylene) but also for handling various polymeric materials such as PC (polycarbonate), PP (polypropylene), and PVC (polyvinyl chloride). This broad compatibility gives the melt pump significant potential for application in the plastics processing industry.
Production of Multiple Plastic Products:
Widely used in plastic extrusion lines, the melt pump is instrumental in producing various plastic products, including granules, films, pipes, sheets, and plates. In the production of PE packaging boards, the melt pump ensures stable pressure and flow of the melt into the extruder head, enhancing product quality and production efficiency.
III. System Stability and Controllability
Isolation of Fluctuations:
In plastic processing, the melt pump is typically installed between the extruder and the die head. This configuration effectively isolates fluctuations originating from the extrusion direction, safeguarding the die head and downstream equipment from any disturbances. Regardless of fluctuations at the pump inlet, as long as the melt entering the pump fully fills the gear grooves, the pump can deliver material to the die head with stable pressure and flow.
Enhanced System Stability:
The use of melt pumps improves the overall stability of the extrusion system, reducing production issues caused by pressure and flow fluctuations. This contributes to higher product yield and consistency.
Increased Controllability:
Melt pumps also enhance system controllability. By adjusting parameters such as pump speed and output pressure, precise control over the extrusion process can be achieved, facilitating automation and intellectualization of the production process.
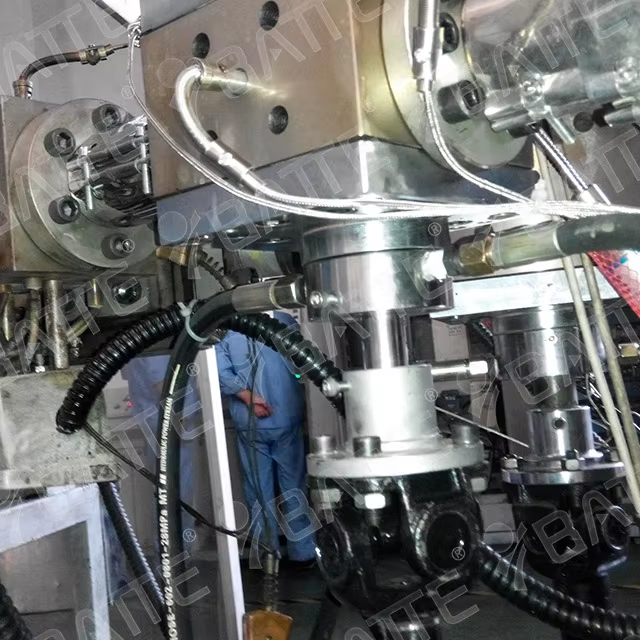
IV. Reduced Energy Consumption and Costs
Lower Energy Consumption:
The high efficiency of melt pumps contributes to reduced energy consumption during production. Compared to alternative methods, using a melt pump can decrease electricity consumption and energy waste while maintaining the same production output.
Extended Equipment Lifespan:
By assuming part of the pressure load from the extruder, the melt pump alleviates the extruder's burden. This helps to prolong the service life of the extruder and other equipment, ultimately lowering the costs associated with equipment replacement and maintenance.
Email: info@battemachinery.com
WhatsApp: +86 158 38331071