How to choose a thermoplastic melt pump for different production lines?
When selecting a thermoplastic melt pump for different production lines, multiple factors need to be taken into consideration to ensure that the chosen pump can meet the specific requirements of the line. The following are some key selection criteria and steps:
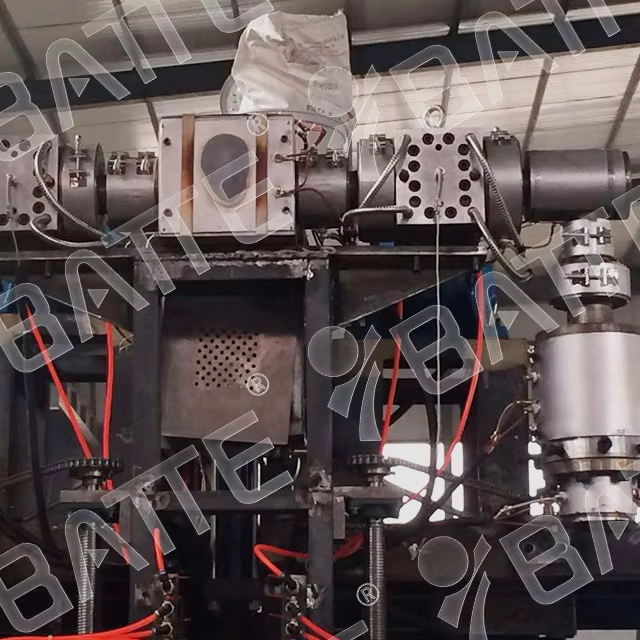
I. Selection Criteria
Material Properties:
Viscosity: Given the wide range of viscosity among different materials, the viscosity range of the material must be considered when selecting a melt pump to ensure smooth material transfer.
Temperature: The operating temperature of the material is also a crucial factor. High-temperature materials require a melt pump that can withstand high temperatures to prevent failure of the pump body materials.
Corrosivity and Toxicity: For materials with corrosive or toxic properties, a melt pump with corresponding corrosion resistance is necessary to ensure production safety.
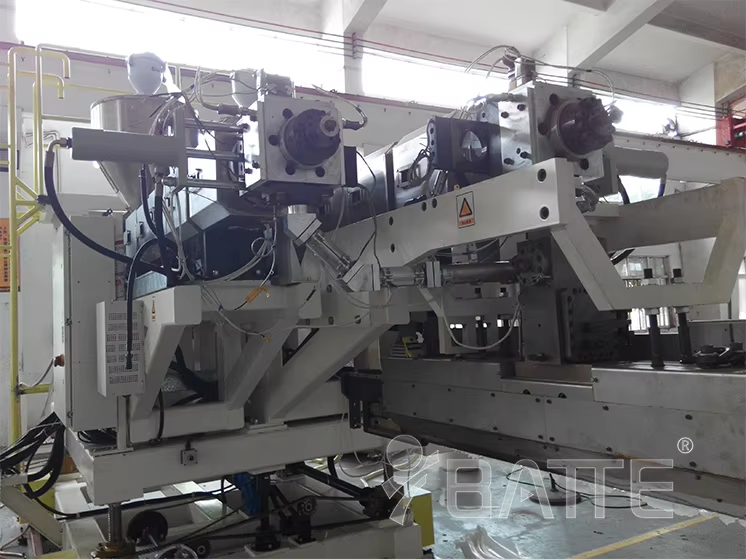
Production Requirements:
Flow Rate: Determine the flow rate range of the melt pump based on the production line's output demands. This is usually related to the pump's displacement capacity (CC) and rotational speed.
Pressure: The production line's pressure requirements for the melt pump are also essential for selection. Ensure that the pump can provide sufficient pressure to meet production needs.
Operating Conditions:
Specific Conditions: Factors such as the production line's layout, space constraints, and operating environment will impact the pump's installation, operation, and maintenance.
Equipment Compatibility: Consider the compatibility of the melt pump with other equipment on the production line, such as extruders and molds, to ensure smooth line operation.
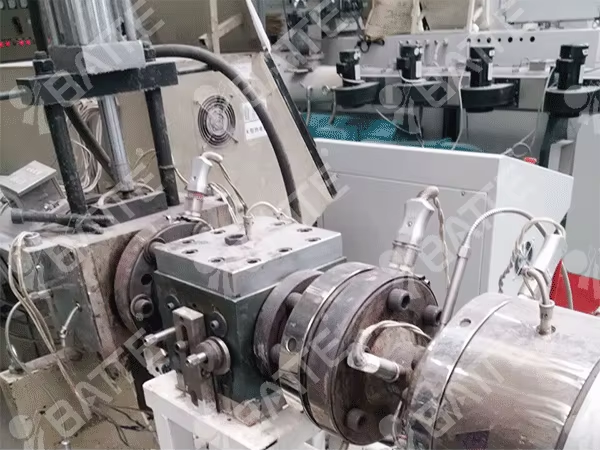
II. Selection Steps
Clarify Needs: Thoroughly understand the material properties, production requirements, and operating conditions of the production line.
Sizing Calculation: Based on material properties and production requirements, calculate the required parameters for the melt pump, including flow rate, pressure, and displacement capacity. Consider the pump's adjustable rotational speed to accommodate varying production stages.
Select Model: Choose an appropriate melt pump model based on the calculation results and selection criteria. Consult the manufacturer's product catalog or seek professional advice for more information.
Evaluate Compatibility: Assess the compatibility of the selected melt pump with other equipment on the production line to ensure seamless line operation.
Determine Purchase: After satisfying all selection criteria and steps, finalize the purchase of the chosen melt pump.
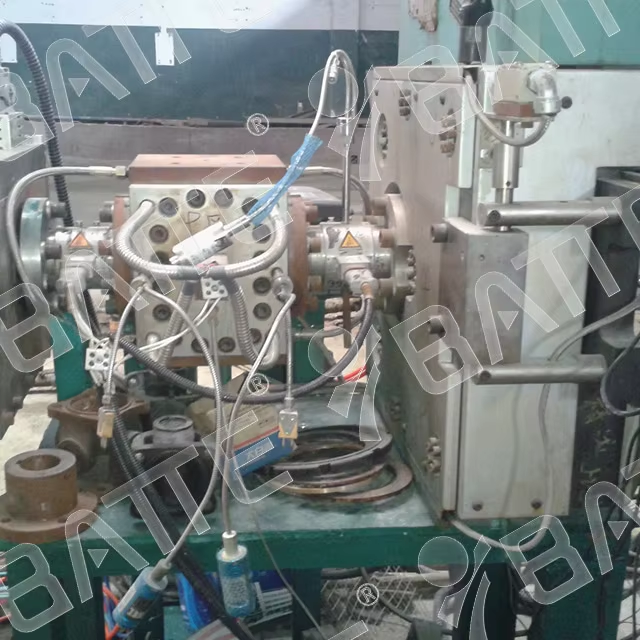
III. Specific Case
Take the PVC pipe production line as an example. PVC is a heat-sensitive material that is prone to carbonization, decomposition, or scorching during extrusion due to temperature fluctuations. Therefore, it is imperative to select a PVC-specific melt pump. These pumps feature a bell-shaped inlet channel, optimized internal flow channels and gear structures, and built-in self-lubrication that allows the lubricant to be expelled with the material. This design is more suitable for PVC's material properties, ensuring smooth line operation and product quality.
In conclusion, selecting a thermoplastic melt pump for different production lines necessitates a comprehensive consideration of material properties, production requirements, and operating conditions, following a clear selection process to ensure that the chosen pump meets the specific needs of the production line.
Email: info@battemachinery.com
WhatsApp: +86 158 38331071