Typical applications of gear pumps in polyester production process - polyester melt gear pumps
The production process of most of today's plastics starts with crude oil. When we talk about crude oil, we generally think of the gasoline that comes from it. In reality, only about 40% of a barrel of crude oil is yielded as gasoline. In order to obtain gasoline and many other useful by-products, petrochemical plants heat crude oil in tanks and separate the various components according to their boiling points. These components are called "fractions", and the process is called "distillation". At a temperature of about 150°C, gasoline is separated from the crude oil, and the gas phase by-products, ethylene and propylene, are "cracked" from the fractions when heated to 840°C and become the raw material for plastics.

These gaseous components, also called monomers, are fed into a reactor. The temperature and pressure inside the reactor varies depending on the polymer produced. The molecular chains of monomers polymerize with each other under heat and pressure to form long chains, which we call polymers. As the reaction proceeds, the heavy mass of polymer sinks to the bottom of the reactor, so the melt gear pump, which is suitable for high temperature, high pressure and high viscosity, comes into play. The melt gear pump for polyester optical film provided by Zhengzhou Batt is designed to solve the problems of uneven material addition, fluctuation of barrel and head temperature, and pulsation of screw speed in the operation of polyester optical film production line.
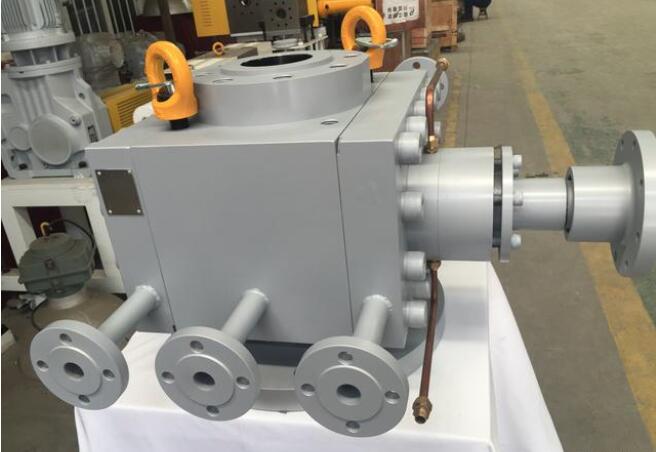
In the operation of the polyester optical film production line, the outlet pressure of the extruder is affected by various factors and there are large pressure fluctuations, which will certainly affect the dimensional accuracy of the extruded cast sheet. The output of the extruder.
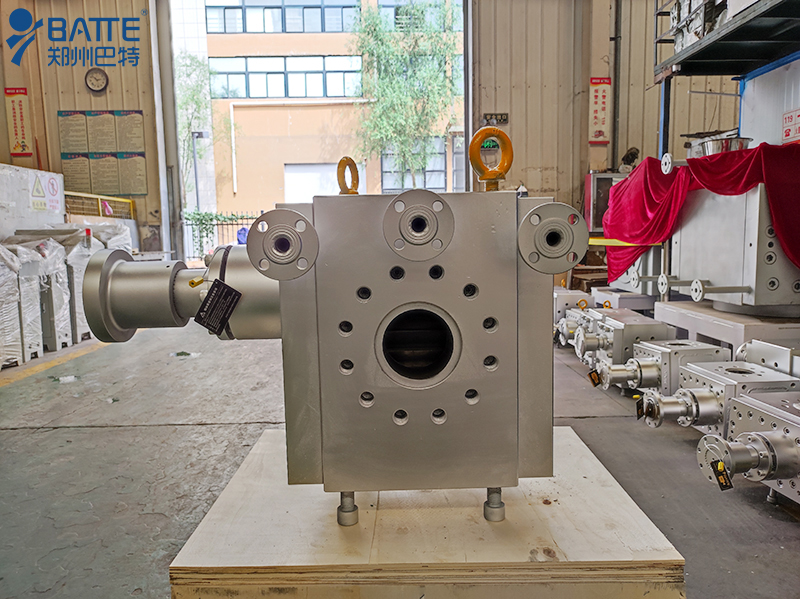
The melt gear pump is used to control the fluid flow of the extruder, and this flow stability directly affects the stability of the whole subsequent process. The melt gear pump is designed with high precision gear gap and volumetric structure, which can achieve stable and balanced extrusion, improve the dimensional accuracy of extruded products and reduce the scrap rate. The use of melt gear pump can eliminate the charging error of the charging system, can greatly reduce the fluctuation of upstream process transmission, quickly enter the stable working condition, improve the dimensional accuracy of extruded products, reduce the scrap rate, improve the output, reduce energy consumption, realize low temperature extrusion, and extend the life of the machine. info@battemachinery.com