What are the benefits of using extrusion melt pumps?
The main function of the extrusion melt pump is to pressurize and stabilize the high-temperature plastic melt from the extruder and send it to the extruder head. Its ability to stabilize melt pressure and flow rate is superior to various types of extruders. When used in tandem with a co-rotating twin-screw extruder, the benefits of the entire production line are significantly increased. The main content of our research and development is to understand the benefits of using melt pumps:
(1) High precision: It can realize stable extrusion, improve the dimensional precision of extruded products and reduce the reject rate. In the extrusion process, the phenomenon of non-uniform material feeding, barrel and head temperature fluctuations, and screw speed pulsation are difficult to avoid. The use of the extrusion melt pump eliminates the feeding error of the feeding system, greatly reduces the upstream process fluctuations, quickly enters a stable working state, improves the dimensional accuracy of the extruded product, and reduces the scrap rate.
(2) Low energy consumption: The co-rotating twin-screw extruder and the extrusion melt pump are combined into a mixing extrusion granulation production line, and their mixing quality and output are significantly higher than those of a twin screw granulator.
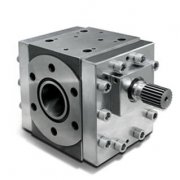
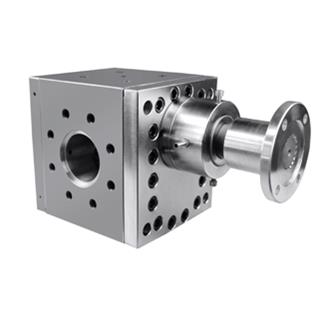
(3) Provincial process: In the original single-screw or twin-screw twin screw extruder, the extrusion melt pump and tube, plate, film and other extrusion heads are installed, which can eliminate the direct extrusion products from the granulation process. This system is ideal for applications where the extruded product material needs to be modified by blending. In addition to the above-mentioned second advantage, the melt pump system also achieves energy saving by simplifying the production process of the extruded product and shortening the production cycle.
(4) Long life: After using the melt pump, the pressure in the screw barrel of the extruder is reduced, which can greatly reduce the wear between the screw and the screw barrel, reduce the load on the thrust bearing of the gear box, and prolong the life of the extruder. The problem of the discharge of the extruder during the production process that requires venting can also be solved.
(5) Easy to detect: With linear extrusion characteristics, it facilitates the coordination of upstream and downstream equipment. Since the gear pump has a low leakage flow, the pump's conveying capacity is basically linear with the rotation speed. After the rotation speed of the gear pump is changed, the flow rate can be exactly known. Because the working speeds of the upstream and downstream equipment and the gear pump can be determined synchronously, the gear pump can be used. The pressure, temperature, and other information collected at the inlet and outlet points enables online monitoring and feedback control throughout the entire extrusion process.